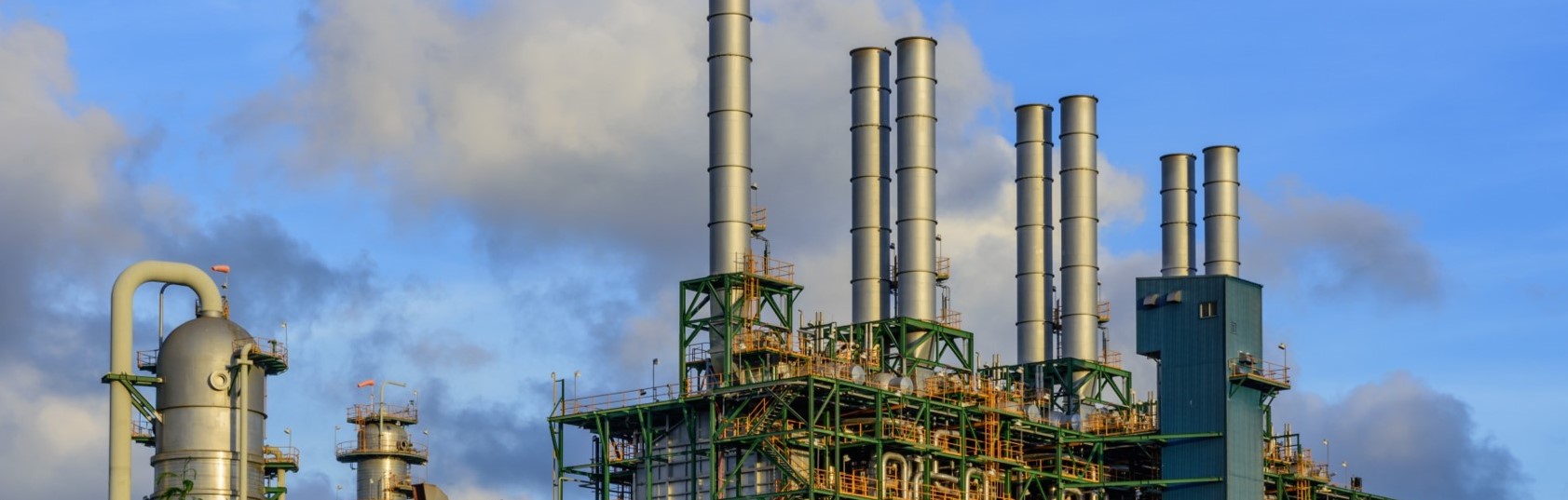
A formação interna de coque em reatores tubulares de craqueamento a vapor de unidades de etileno tem grande influência na eficiência energética e na viabilidade econômica do processo. Quando o coque é formado dentro das serpentinas de craqueamento a vapor, resulta em uma maior queda de pressão, alterando a extensão operacional e a seletividade do produto da unidade. Devido à formação de coque, a temperatura do tubo metálico (TMT) aumenta com o tempo, eventualmente exigindo que o forno seja desligado para "descoqueamento", levando à perda de produção e maior consumo de energia e custos de manutenção.
Muitos esforços têm sido feitos nos últimos anos para desenvolver tecnologias para reduzir a formação de coque. A Veolia desenvolveu um novo revestimento catalítico patenteado, chamado YieldUp, que possui uma estrutura química exclusiva capaz de converter coque em óxidos de carbono em contato.
O inovador revestimento YieldUp foi aplicado aos novos tubos de forno a serem instalados em um craqueador a vapor de etileno europeu de 30 T/h, que usava diferentes tipos de matéria-prima (por exemplo, nafta, GLP e butano), para determinar sua eficiência e durabilidade. Os tubos revestidos foram usados por um período de 36 meses para determinar se isso reduziria a frequência de descoqueamento, que antes era feito a cada 40 dias com tubos não revestidos.
Figura 1: Tubo de forno revestido YieldUp
YieldUp é um revestimento catalítico patenteado desenvolvido pelo nosso Centro de Pesquisa e Desenvolvimento.
O revestimento passiva os locais cataliticamente ativos da liga do reator, reduzindo o acúmulo de depósito de coque catalítico. Ele impulsiona a conversão do coque depositado em CO2 e hidrogênio por meio da gaseificação, reagindo com vapor de alta temperatura.
As novas bobinas instaladas no craqueador de etileno europeu foram revestidas com uma camada de 25μmde YieldUp, que foi então sinterizada na superfície interna da bobina. As bobinas então foram montadas, soldadas e instaladas no craqueador a vapor.
Enquanto operava com os tubos recém-revestidos, o forno processava várias matérias-primas. Isso permitiu monitor a formação de depósitos de coque que ocorria sob várias condições operacionais.
Resultado
O principal indicador de desempenho da eficácia e desempenho do revestimento consiste no perfil da temperatura do metal do tubo (TMT) durante a execução (Figura 2).
Figura 2: Monitoramento da TMT de forno com tubos revestidos
A TMT inicial durante o reinício, após a decoqueificação, foi consistentemente menor em uma faixa de 10-20°C (18-36°F). Como esperado, a curva TMT durante toda a execução foi mais plana do que para um forno sem revestimento, o que resultou em uma extensão do comprimento da execução do forno até a TMT máxima de 1120°C (2250°F) fosse alcançada.
A prova da eficácia do YieldUp pode ser observada após cada ciclo de descoque como picos de CO2, indicando a gaseificação do coque catalítico e a redução da formação de depósitos nos tubos.
As análises metalúrgicas também foram realizadas nos tubos tratados depois de 9 meses de operação e vários ciclos de descoqueamento, confirmando a presença do revestimento e, portanto, sua durabilidade após várias execuções.
Durante os 36 meses de operação com os tubos revestidos de YieldUp, a frequência de descoqueamento do forno foi reduzida pela metade, dobrando efetivamente os comprimentos de execução de um parâmetro de menos de 40 dias para uma média de quase 80 dias (Figura 3).
Figura 3: período de execução entre o descoqueamento do forno europeu
A economia de combustível associada ao aumento da eficiência da transferência de calor e à redução da frequência de descoqueamento foi estimada em ~3%, economizando aproximadamente 500.000€ por ano e eliminando a emissão de ~3000 T/ano de CO2. A redução na frequência de descoque também proporciona mais tempo de atividade, aumentando a produtividade da fábria em cerca de 3%. Espera-se também prolongar a expectativa de vida da bobina devido à menor fluência e carbonetação, representando ganhos operacionais significativos.